The typical roller plating process is as follows: small parts that have undergone pre-plating treatment are loaded into the drum. The parts rely on their own gravity to tightly press the cathode conductive device in the drum to ensure that the current required for the parts to be plated can be transmitted smoothly. Then, at the same time, the main metal ions are reduced to a metal coating on the surface of the parts after being affected by the electric field. Fresh solution outside the drum is continuously replenished into the drum through countless small holes on the drum wall, and the old solution in the drum and the hydrogen generated during the electroplating process are also discharged from the drum through these small holes.
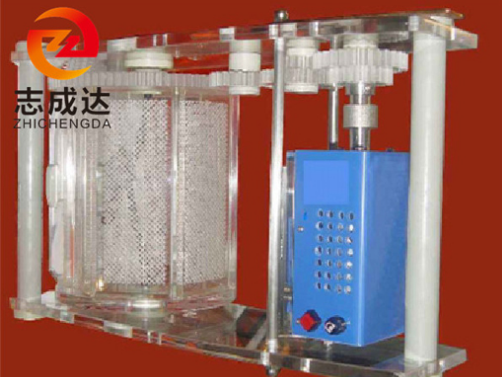
Strictly speaking, barrel plating is called drum electroplating. It is a kind of electroplating processing method that places a certain number of small parts in a special drum, and deposits various metal or alloy coatings on the surface of the parts in an indirect conductive manner in a rolling state to achieve surface protection, decoration and various functional purposes. The typical barrel plating process is as follows: the small parts that have been pre-plated are loaded into the drum, and the parts rely on their own gravity to tightly press the cathode conductive device in the drum to ensure that the current required for the parts to be plated can be smoothly transmitted. Then, at the same time, the main metal ions are reduced to metal coatings on the surface of the parts after being affected by the electric field, and the fresh solution outside the drum is continuously replenished into the drum through the countless small holes on the drum wall, and the old solution in the drum and the hydrogen generated during the electroplating process are also discharged from the drum through these small holes.