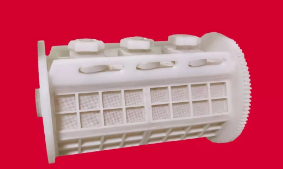
As shown in Figure 1, during barrel plating, it can be considered that only the surface parts are plated, while the inner parts are not plated due to the shielding and blocking of the surface parts. But the actual situation is that the inner parts are not completely unplated, but the smaller the current density of the parts is towards the center, the weaker the plating effect is, until it may not be plated at all. Just for the convenience of analysis and discussion, it is assumed that the inner parts are completely unplated.
At this time, the inner parts only play the role of current transmission, which is equivalent to ordinary electronic conductors. In order to have a chance to be plated, the inner parts need to be turned out from the “diagonal area” to become the surface parts, and the faster and more evenly they are turned out, the higher the efficiency of plating and the better the plating quality. However, after the surface parts are plated for a while, they will quickly turn back to the “diagonal area” to become the inner parts. Because there are always inner parts that need to be turned to the surface for plating, the surface parts cannot stay in their position for a long time. In this way, only by constantly rolling and mixing small parts can the inner and surface parts be constantly changed and converted, and finally every part can be plated evenly.
In this case, whether the small parts can be fully separated and quickly displaced during roll plating is very critical. Separation refers to the separation and combination of parts from time to time. The purpose is to make the inner and surface parts easily change and convert, and not shield or block each other after becoming surface parts, resulting in defective products. For example, screws and nuts, if the parts can be clearly separated, they can be easily turned to the surface for plating. However, for parts that are easy to entangle, such as fish hooks, springs, and guide pins, the rotation of the roller not only cannot make them fully separated, but may also make the entanglement more serious, so it is not easy to achieve a rapid conversion between the inner and surface parts, which brings difficulties to the roll plating method. For the parts shown in Figure 2, multiple parts are easy to hold together during roll plating. If the separation is not clear and they are finally “locked”, even if they are turned to the surface, they will inevitably become defective. If the defective rate is too high, it is not suitable for roll plating.
Displacement refers to the constant change of position between the inner and surface parts, the purpose is to make the inner parts constantly turn out and become surface parts for plating. Moreover, the faster the displacement action, the more conducive it is to improve the quality of the parts coating and the efficiency of plating. Obviously, the role of displacement is very important, which goes without saying for ordinary parts such as screws and nuts, and is even more important for some special parts. For example, deep and blind hole parts such as battery steel shells and crystal resonator shells require that the inner and surface parts can be displaced quickly, otherwise the solution in the hole cannot be updated in time and the coating quality cannot be guaranteed. The surface of NdFeB parts is very easy to oxidize. When pre-plating or direct plating is required, the parts should be plated as quickly as possible in the drum to suppress the poor bonding strength of the coating caused by oxidation of the substrate. If the inner and surface parts cannot be displaced quickly, the surface of the parts cannot be plated as soon as possible. When the parts are located in the inner layer, the substrate will inevitably oxidize, resulting in poor bonding strength of the subsequent coating.
Therefore, clutch and displacement are two very important concepts of roller plating, and are necessary conditions for whether small parts can be roller plated.