The importance of electroplating equipment selection for electroplating quality
The selection of electroplating equipment is of key significance to ensure the quality of electroplated products and improve production efficiency. This article introduces in detail the circular automatic electroplating line, program-controlled gantry electroplating line and roller plating automatic production line, as well as the supporting peripheral equipment such as rectifiers, filters, heat exchangers, ultrasonic cleaning machines and additive automatic adding machines.
I. Advantages of circular automatic electroplating line:
- High degree of automation, high efficiency, reduced labor intensity, fewer operators;
- Lever-type vertical lifting, high utilization rate of plating tank capacity;
- Short exposure time, stable operation of workpieces, and each arm time of about 20 to 100 seconds;
- It is suitable for electroplating with high coating quality requirements, large batches, relatively simple shapes, and mature processes. The light mechanical circular electroplating production line (commonly known as the hanging fish type) is very popular due to its low price, light weight, easy maintenance, and high output.
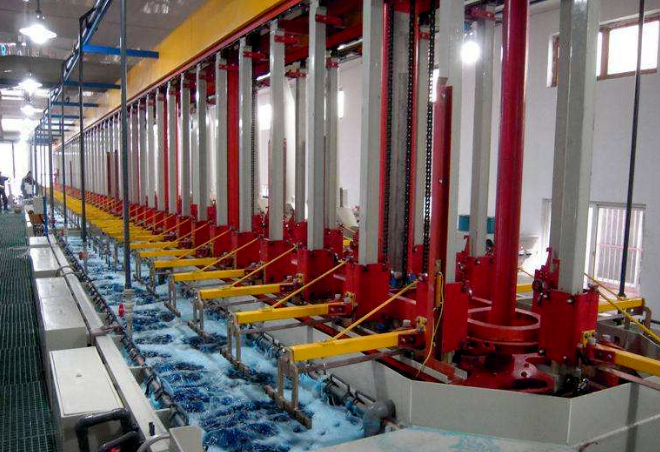
- Program-controlled gantry electroplating line:
- High degree of automation, high efficiency, reduced labor intensity, and fewer operators;
- Suitable for electroplating of heavier parts and large objects, and also suitable for electroplating of parts of different shapes and batches;
- Convenient change of driving working conditions, flexible control of electroplating time, suitable for electroplating of various production processes;
- Excellent and stable electroplating quality. Suitable for processes requiring thicker coatings.
- Roller plating automatic line:
Roller plating automatic lines also have two categories: circular mechanical or hydraulic automatic lines and linear gantry automatic lines.
Circular mechanical bell-shaped roller high-speed electroplating equipment (sheets, wires) and selective electroplating equipment suitable for tilting automatic loading and unloading.
With the development of the economy and the progress of electronic electroplating, the demand for high-speed electroplating production automatic lines and selective electroplating production lines has increased. Most of them are undertaken by companies with greater technology and manufacturing capabilities.
- Auxiliary equipment around electroplating production line:
- Electroplating power supply:
The electroplating power supply is the most important auxiliary equipment in the electroplating production process. Silicon rectifiers and thyristor rectifiers are widely used in China, which are divided into voltage regulator, magnetic saturation reactor and thyristor.
Silicon rectifiers and thyristor rectifiers for electroplating are low-voltage and high-current, generally 12V (18V for chrome plating). There are silicon rectifiers with thyristor voltage regulation from 100A to 20000A. Only electroplating power supplies with good current and voltage stability and stable current density when the load is high are being promoted and applied.
- Electroplating solution filtration equipment:
The filter is one of the key equipment related to the quality of electroplating products. Both filter elements and filter cloths can be produced. Pay attention to the “real” filtration accuracy when choosing.
There are still some problems in the production of filters:
(1) The standardization and high reliability of filter machines for chrome plating and chemical nickel plating need to be studied. Special plastics such as polyvinylidene fluoride (PVDF) and chlorinated polyvinyl chloride (CPVC) and related parts must be introduced. Polypropylene plastic cannot be used to make chrome-plated filters.
(2) High-quality magnetic pumps need to be developed.
(3) The filtration accuracy provided by the factory now needs to be verified by scientific means. Special filter cloth, filter bag and filter paper need to be produced.
(4) The shaft seal material of the centrifugal filter needs to be improved, and the problems of wear resistance and leakage prevention should be solved.
(5) The electroplating process is changing with each passing day, and auxiliary equipment must keep up. For example, the pre-treatment special chemical degreasing filter can not only separate the floating oil on the liquid surface, but also absorb the suspended oil droplets. It will greatly improve the quality of electroplating products and the quality of phosphating film.
- Application of ultrasonic equipment
The cavitation effect of ultrasonic waves can greatly speed up the degreasing and rust removal of pretreatment, shorten the processing time, and improve the degreasing and rust removal effect.
- Heating and cooling equipment
Traditional electroplating heating methods mostly use steam or electric heating. Refrigeration units are generally used in summer to ensure that acid bright copper and bright tin plating work at standard operating temperatures.
- Automatic management system for electroplating solution
The automatic management system for solution is a device for detecting and controlling solution composition and process parameters.